When it comes to ensuring that cold rooms operate flawlessly, Emiratefix Cold Room Repair in Dubai stands out as a leader in Dubai. With a strong focus on providing high-quality and efficient repair solutions, the company understands the vital role that cold rooms play in various sectors, from hospitality to food distribution and retail.
What sets Emiratefix apart is its commitment to customer satisfaction, offering 24/7 service to address urgent repair needs. Their team of skilled technicians specializes in diagnosing and fixing cold room issues rapidly, ensuring that businesses remain operational and compliant with health standards. Each technician is well-trained in handling the advanced technology that modern cold rooms utilize, making them well-equipped to deal with any challenges that arise.
Here’s a brief overview of the services provided:
- Cold Room Troubleshooting and Diagnosis
- Repairing Faulty Compressors
- Fixing Insulation Problems
- Quality Replacement Parts and Equipment
With Emiratefix, customers can expect not just expertise, but a combination of prompt service and the use of authentic replacement parts. This approach minimizes downtime and helps maintain the integrity of items stored within the cold room.
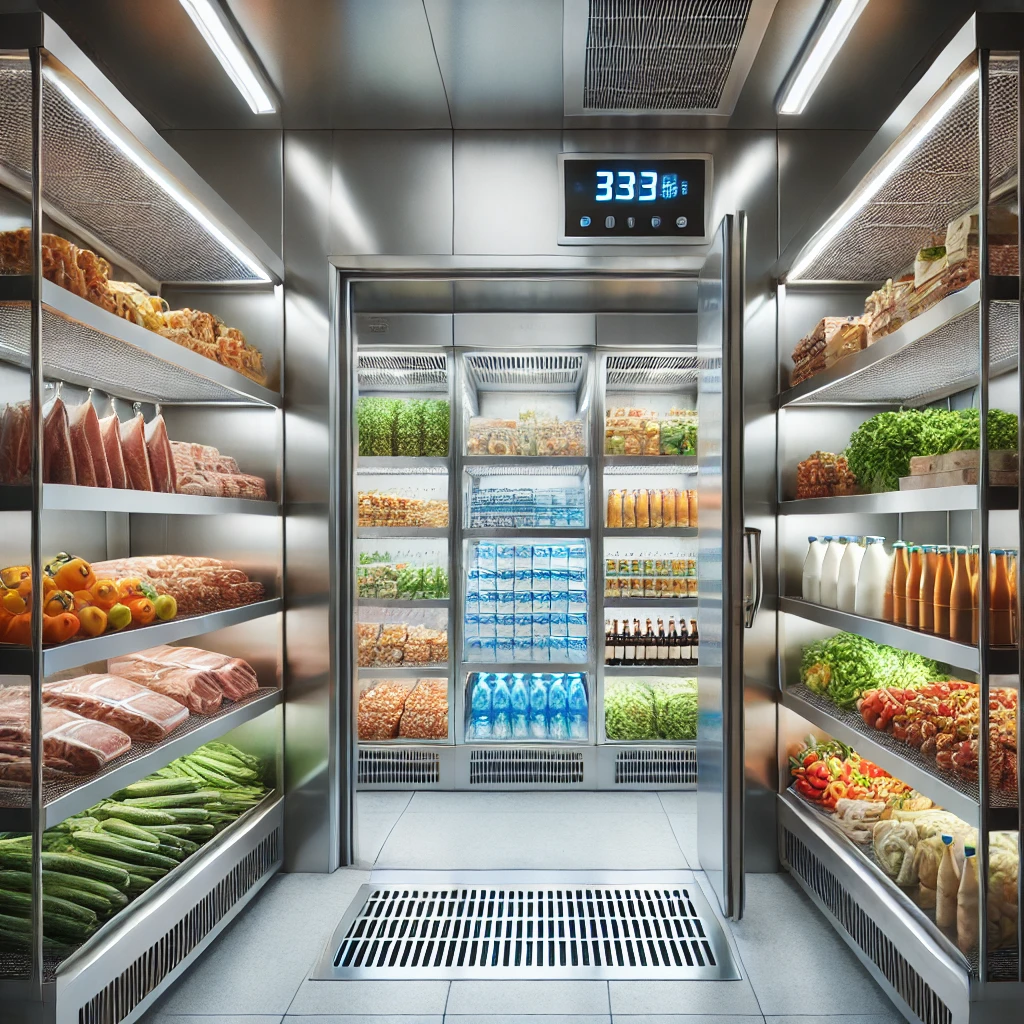
Fast & reliable cold room repair in Dubai! Ensure optimal cooling performance—contact us today for expert service!
Importance of Maintaining Cold Rooms in Dubai
In a bustling city like Dubai, where temperatures can soar, maintaining cold rooms is crucial for various reasons. The high ambient temperatures present unique challenges for businesses that rely heavily on refrigeration. Here are a few important aspects to consider:
- Food Safety and Quality
- Cold rooms are essential for storing perishable goods. Proper maintenance ensures that temperature is consistently regulated, preventing spoilage. For example, a local restaurant faced a crisis when their cold storage malfunctioned, leading to the costly disposal of spoiled ingredients—money that could have been saved with timely repairs.
- Energy Efficiency
- Efficient cooling systems lead to significant cost savings on energy bills. Regular maintenance checks can identify potential issues before they escalate, ensuring that the system runs smoothly. When cold rooms operate at optimal efficiency, they consume less energy, which is both eco-friendly and cost-effective.
- Compliance with Health Regulations
- Dubai has strict health and safety regulations, particularly in the food and beverage sector. Failing to maintain cold storage can lead to non-compliance, resulting in penalties or even business closures. Timely cold room repairs can help businesses stay within legal guidelines, protecting their operations and reputation.
- Extended Equipment Lifespan
- Regular maintenance not only prevents breakdowns but also extends the life of expensive refrigeration machinery. By investing in repair services from the onset, businesses can avoid the high costs associated with replacing failing equipment.
- Disruption Minimization
- For businesses that operate 24/7, any downtime can be detrimental. Cold room failures can lead to lost revenue and unhappy customers. An example worth noting involves a supermarket chain that experienced significant losses during hot days due to refrigeration leaks. However, with prompt repair services from Emiratefix, they managed to rectify the situation quickly, minimizing their losses.
In selection, understanding the critical importance of maintaining cold rooms in Dubai cannot be overstated. From preserving food safety to ensuring compliance with local regulations, the impact that properly functioning cold rooms have on businesses is profound. Emiratefix Cold Room Repair Services provides a reliable lifeline to businesses, combining expertise with fast response to safeguard their refrigerated assets.
Reflecting on these points, it becomes clear why proactive maintenance and regular repairs are necessary for cold room longevity and efficiency.
Common Cold Room Issues
Refrigeration System Breakdowns
While cold rooms play a critical role in preserving perishable goods and ensuring the smooth operation of businesses, they are not invincible. One of the most common issues encountered is refrigeration system breakdowns. These breakdowns can stem from various causes, often leading to significant disruptions and financial losses.
Imagine your restaurant’s cold room suddenly breaking down in the middle of a busy dinner service; the panic sets in as staff scramble to find a solution before precious ingredients spoil. Unfortunately, this scenario is quite prevalent. A study conducted among local businesses highlighted that nearly 30% of cold room failures are due to unforeseen mechanical issues. Here are some typical causes of refrigeration system breakdowns:
- Compressor Failure: The heart of the refrigeration system, the compressor, can fail due to wear and tear, leading to inadequate cooling. Without a functioning compressor, temperature control becomes impossible.
- Electrical Failures: Issues like tripped circuit breakers or faulty wiring can halt the cooling process altogether. Given Dubai’s high temperatures, a sudden electrical issue can result in rapid spoilage.
- Condenser Coil Issues: Debris buildup on condenser coils can restrict airflow, severely impacting efficiency. Regular cleaning can often prevent this issue, but neglect can lead to breakdowns.
- Refrigerant Leaks: The presence of refrigerant is necessary for cooling. Any leaks not only lead to inefficiency but can also pose environmental hazards.
Taking proactive steps can mitigate these issues. Regular maintenance through a service like Emiratefix can help identify potential problems before they escalate, ensuring that the cold room continues to function as anticipated.
Temperature Fluctuations
Another major challenge that businesses face with cold rooms is temperature fluctuations. Consistency is key when it comes to preserving the quality of perishables. Fluctuations can lead to food spoilage, affecting quality and safety, and can severely impact revenue.
Picture a bakery that distributes pastries across Dubai. If their cold room experiences sudden temperature changes, the result could be an entire batch of spoiled pastries ready for delivery. This not only affects profits but can also damage a bakery’s reputation. Some common reasons for temperature fluctuations include:
- Insufficient Insulation: If insulation is faulty or deteriorated, outside temperature can seep in, disrupting the controlled environment. This is often an overlooked factor that can cause serious harm to the cold room’s integrity.
- Malfunctioning Thermostat: If a thermostat isn’t calibrated correctly or malfunctions, it can lead to inaccurate temperature readings. This means that even if the cold room seems to be running fine, it might not be maintaining the ideal temperature.
- Overloading the Cold Room: Packing too much into a cold room can block airflow and lead to uneven cooling. Effective inventory management is crucial here to avoid overloading and the subsequent risks that come with it.
- Frequent Door Openings: Particularly in busy establishments, constant openings of cold room doors can let warm air inside, creating drastic temperature variations. Training staff to minimize open door time can make a significant difference.
To mitigate these issues, regular inspections and repairs from Emiratefix can ensure equipment operates at peak efficiency while maintaining a stable environment. Implementing consistent management practices can further support temperature control.
In conclusion, understanding and addressing common cold room issues such as refrigeration system breakdowns and temperature fluctuations is vital for business longevity and success. Prompt repairs and proper maintenance are essential, helping businesses avoid loss and continue operating smoothly.
Emiratefix Repair Services
Cold Room Troubleshooting and Diagnosis
When it comes to maintaining the efficiency of cold rooms, expert troubleshooting and diagnosis can make all the difference. Emiratefix provides top-notch services aimed at identifying and resolving such problems promptly to ensure your cold room operates smoothly.
Imagine the stress of discovering that a cold room is not maintaining its required temperature just before a major catering event. The good news is that Emiratefix is just a call away, ready to tackle these urgent issues head-on.
The troubleshooting process begins with a thorough examination of the cold room’s components. Trained technicians utilize specialized diagnostic tools to assess the refrigeration system, inspecting aspects such as:
- Electrical Connections: Ensuring there are no faults in wiring or inefficiencies in power supply.
- Thermostat Calibration: Verifying that temperature settings are accurate for optimal performance.
- Airflow Systems: Checking for blockages that could impede efficient air circulation within the cold room.
- Condenser and Evaporator Coils: Assessing coils for dirt or damage that may restrict heat exchange processes.
Once the diagnosis is complete, the technicians provide a detailed report of identified issues along with tailored recommendations to restore functionality. Keeping business operations running smoothly is the priority, and with Emiratefix’s swift response, you can be assured of minimum disruption.
Repairing Faulty Compressors
The compressor is a fundamental component of any refrigeration system, often regarded as its heart. A fault in this critical machinery can bring operations to a grinding halt, resulting in both financial loss and potential spoilage of goods.
At Emiratefix, repairing faulty compressors is treated with utmost priority due to the importance of maintaining a stable temperature. When compressors fail, the technicians take a systematic approach that entails:
- Compressor Inspection: Evaluating components for wear and tear, including checking for unusual sounds or vibrations that may indicate malfunction.
- Identifying Leakage: Assessing for refrigerant leaks and ensuring that the compressor maintains its integrity.
- Re-calibration: Ensuring that the compressor is running at optimal pressure levels for effective cooling.
For example, a local grocery store once called upon Emiratefix for compressor issues during peak business hours. The technicians arrived promptly, diagnosed a faulty component, and repaired the compressor on the spot, ultimately saving thousands of dirhams in spoiled inventory.
By investing in repairs from professionals like Emiratefix, businesses can enhance the reliability of their refrigeration systems, reduce energy costs, and prolong the lifespan of their equipment.
Fixing Insulation Problems
Insulation plays a crucial role in the efficiency of cold rooms by preventing the exchange of warm air from outside. If insulation is compromised, it can lead to severe temperature fluctuations and increased energy costs.
Emiratefix specializes in identifying and fixing insulation problems efficiently. Their methodology typically includes:
- Visual Inspections: Assessing seals, doors, and insulation panels for gaps or wear.
- Thermal Imaging: Using specialized equipment to detect cold spots that indicate insulation deficiencies.
- Seal Repairs or Replacements: Ensuring that all joints and edges are properly sealed to avoid air leakage.
For instance, a restaurant that recently upgraded its refrigeration system faced constant temperature issues. A follow-up inspection revealed that old insulation was the culprit. Emiratefix technicians swiftly replaced the insulation, providing immediate improvements in temperature regulation and energy efficiency.
This attention to detail with insulation not only boosts operational efficiency but also correlates with significant cost savings on energy bills over time.
In conclusion, Emiratefix offers a comprehensive suite of repair services tailored to address specifics like cold room troubleshooting, compressor repairs, and insulation fixes. These services are instrumental in ensuring cold rooms remain reliable and efficient, minimizing disruption and protecting investments in inventory. Trusting Emiratefix means your business can continue to operate smoothly, even in the hottest conditions.
Benefits of Timely Cold Room Repairs
Ensuring Food Safety and Quality
When it comes to the hospitality and food distribution sectors, ensuring food safety and quality is paramount. Timely cold room repairs play a crucial role in safeguarding perishable goods, and it’s a responsibility that business owners cannot afford to overlook.
Imagine a bustling restaurant preparing for a large banquet, only to discover that their cold room is not maintaining an adequate temperature. Not only does this jeopardize the freshness of the ingredients, but it can also lead to serious health risks for customers. Bacteria can thrive when food is stored above the appropriate temperatures, leading to spoilage and potential foodborne illnesses.
Here are a few ways timely cold room repairs contribute to food safety and quality:
- Prevent Spoilage: Regular maintenance and prompt repairs ensure that food is kept at the safe temperature required to prevent spoilage. This preserves the quality and longevity of ingredients, which is crucial for any food business.
- Compliance with Health Regulations: Different regions, including Dubai, have stringent health codes related to food safety. Ensuring that cold rooms are in optimal condition means staying compliant with these regulations, thus avoiding fines or legal repercussions.
- Maintaining Freshness: Customers expect high standards, particularly when dining out or purchasing fresh food. Timely cold room repairs help maintain texture, flavor, and nutritional value, enhancing customer satisfaction.
- Enhancing Reputation: Businesses known for their commitment to food safety build trust and loyalty among their clientele. A single incident of spoiled food could tarnish a brand’s reputation, but by being proactive, the risk of such incidents diminishes significantly.
In summary, taking swift action on cold room repairs is vital to ensure that food safety is not compromised. Emiratefix plays an essential role in this process, providing businesses with the support they need to maintain their operations with confidence.
Cost Savings on Energy Bills
Another significant advantage of timely cold room repairs is the cost savings on energy bills. In a city like Dubai, where temperatures can skyrocket, an efficiently operating cold room is not just a matter of safety—it’s also fundamental for streamlining operational costs.
Consider a scenario where an establishment inadvertently ignores minor issues, such as a malfunctioning thermostat or dirty condenser coils. These small problems can lead to increased energy consumption as the system struggles to maintain the desired temperature. When repairs are delayed, the result can be startling—up to a 30% increase in energy costs, according to some industry reports.
Here are the key reasons how timely cold room repairs contribute to cost savings:
- Optimized Efficiency: Well-maintained cold rooms operate efficiently, consuming less energy. When components are in good working order, the refrigeration system doesn’t have to work overtime, resulting in lower utility bills.
- Reduced Repair Costs: Addressing issues early can prevent more significant problems from developing, which often leads to higher repair costs down the road. Investing in small repairs today can save businesses from the financial burden of major breakdowns tomorrow.
- Longer Equipment Life: Regular servicing and repairs extend the lifespan of expensive refrigeration equipment. With proper maintenance, businesses can avoid costly replacements and continue to benefit from their initial investments for years.
- Increased Productivity: With a reliable cold room, staff can dedicate their time to serving customers rather than constantly handling refrigeration issues. Better operational efficiency reflects positively in overall revenue.
For instance, a grocery store experienced escalating utility bills without realizing that inadequate maintenance was the culprit. After calling in Emiratefix for repairs, the technicians discovered multiple inefficiencies led to energy wastage. Post-repair, the store saw a 20% reduction in energy costs, thus ensuring considerable savings month after month.
In conclusion, investing in timely cold room repairs brings forth substantial benefits ranging from food safety and quality assurance to significant cost savings on energy bills. Whether it’s preserving the freshness of perishable goods or streamlining operational costs, businesses can rely on Emiratefix to help them achieve these vital objectives efficiently.
Choosing Emiratefix for Cold Room Repairs
Experienced Technicians
When it comes to cold room repairs, choosing Emiratefix means putting your trust in a team of experienced technicians. Their expertise is one of the main reasons businesses across Dubai rely on their services for maintaining optimal cold room efficiency.
Navigating the complexities of refrigeration systems requires a deep understanding of both the technology and the common issues that can arise. Technicians at Emiratefix are not only highly trained but also bring years of hands-on experience to the table, making them well-equipped to tackle a variety of challenges.
For example, consider a major hotel in the heart of Dubai. Due to a malfunctioning cold room, they were struggling to keep high-quality ingredients fresh for their acclaimed restaurant. When Emiratefix was called in, the experienced technicians quickly identified a faulty compressor as the culprit. Their swift and knowledgeable response not only resolved the issue within hours but also prevented what could have been a significant loss of inventory.
Here’s what sets Emiratefix technicians apart:
- Certifications and Training: Each technician undergoes rigorous training and certification to ensure they’re current with industry standards and practices.
- Proven Track Record: With countless successful repairs under their belts, these technicians can troubleshoot and resolve issues efficiently—saving time and minimizing downtime for your business.
- Customer-Centric Approach: They not only fix problems; they educate business owners about maintaining their equipment. This empowers clients to take a proactive stance on cold room management.
- 24/7 Availability: Cold room issues don’t adhere to a 9-to-5 schedule. Emiratefix offers round-the-clock service, ensuring that businesses can get the support they need whenever an emergency arises.
By choosing Emiratefix, businesses gain not just repair services, but a team of skilled professionals dedicated to keeping operations running smoothly.
Quality Parts and Equipment
In addition to having skilled technicians, another compelling reason for choosing Emiratefix is their commitment to using quality parts and equipment for repairs. It’s essential to understand that using inferior parts can compromise the effectiveness of repairs and lead to further issues down the line.
For instance, a restaurant that opted for a cheap replacement part during a cold room repair saw its cooling system fail again just weeks later. This unfortunate choice resulted in spoilage of thousands of dirhams worth of perishable goods. Instead, when partnering with Emiratefix, clients receive:
- Original Manufacturer Parts: Emiratefix understands that using OEM (Original Equipment Manufacturer) parts guarantees compatibility and maintains the integrity of the refrigeration system.
- High-Quality Components: Their commitment to quality ensures that businesses can count on repairs lasting longer and performing better, which translates to fewer breakdowns and lower long-term costs.
- Reliable Suppliers: Emiratefix has established relationships with trusted suppliers to ensure that all parts adhere to safety and quality regulations. This careful selection process is part of what makes their service stand out.
- Comprehensive Warranty: Clients can have peace of mind knowing that Emiratefix stands behind their work. Many repairs come with a warranty on both labor and parts, adding an additional layer of assurance.
As an example of their focus on quality, a supermarket chain facing repeated condensation issues chose Emiratefix for a comprehensive assessment. The technicians not only identified the cause but replaced the faulty parts with high-quality alternatives. Not only did this eliminate the condensation problem, but it also led to significant savings on energy bills due to increased efficiency.
In conclusion, choosing Emiratefix for cold room repairs offers businesses the benefits of experienced technicians and an unwavering commitment to quality parts and equipment. By prioritizing expertise and reliability, Emiratefix ensures that your cold room operates effectively, maintaining food safety and optimizing energy costs. This holistic approach sets them apart as a leader in cold room repair services in Dubai, making it a wise choice for any business that relies on cold storage.
Maintenance Tips for Cold Rooms
Regular Cleaning and Defrosting
Maintaining a cold room goes beyond just addressing issues when they arise. Implementing consistent practices such as regular cleaning and defrosting is vital in ensuring optimal performance and longevity of the refrigeration system. Neglecting these tasks can lead to costly repairs down the line, making it essential for business owners to stay proactive.
Cleaning and defrosting not only improve efficiency but also enhance food safety. Here’s why these maintenance tasks matter:
- Prevent Buildup of Ice and Frost: Over time, internal components can accumulate ice and frost, which can obstruct airflow and cause the unit to work harder than necessary. Regular defrosting helps maintain efficient operation by allowing the system to run smoothly.
- Promote Energy Efficiency: A clean cold room operates more efficiently. When coils and vents are clear of debris, the refrigeration system doesn’t have to struggle to maintain temperature, which translates to lower energy bills.
- Uphold Health Standards: For businesses in the food industry, cleanliness is crucial. Regular cleaning of surfaces and inspection for leaks or food debris helps prevent bacterial growth and keeps food safe for consumption.
- Enhance the Lifespan of Equipment: Consistently performing these tasks can extend the life of equipment. By eliminating dirt, grime, and frost, you lessen wear and tear on the refrigeration system, allowing it to function at peak performance longer.
Here’s a quick checklist to follow for effective cleaning and defrosting:
- Schedule Regular Cleaning: Aim for a monthly deep clean that includes surfaces, shelves, and walls. Use approved cleaning agents and ensure that all areas are cleaned thoroughly.
- Inspect and Remove Ice Buildup: Depending on the environment and cold room usage, check for ice accumulation regularly. If you see significant frost buildup, schedule a defrosting session.
- Sanitize Frequently: Ensure that not just cleaning but sanitization is done regularly to maintain hygiene.
- Date and Label Items: Regularly check and remove expired items. Keeping your cold room organized helps in the cleaning process and ensures that inventory is rotating properly.
Incorporating these practices will not only enhance the performance of the cold room but also create a safer working environment.
Monitoring Temperature Levels
Another critical aspect of cold room maintenance is monitoring temperature levels. Ensuring that your system consistently maintains the appropriate temperature is essential for preserving food quality and safety. Here are some practical strategies to effectively monitor temperature levels:
- Use Reliable Thermometers: Invest in high-quality, reliable thermometers that can provide accurate readings. Digital thermometers with alarms that notify when temperatures go beyond acceptable limits can be particularly useful.
- Regular Temperature Checks: Make it a habit to check temperature levels multiple times a day, especially during peak times. Record these levels in a log to spot trends and potential issues over time.
- Calibrate Equipment: Ensure that thermometers and temperature monitoring devices are calibrated correctly. Periodic calibration keeps the readings accurate.
- Set Alert Systems: Consider implementing an alert system that notifies you if the temperature rises or falls beyond set parameters. Some advanced systems can send alerts directly to your smartphone, allowing you to respond swiftly to issues.
- Monitor Door Openings: Frequent door openings can affect temperature stability. Educate your staff on minimizing door open times and using the cold room efficiently.
- Conduct Routine Inspections: Regularly inspect seals, hinges, and door closures to prevent warm air from entering. Ensuring that doors close securely is crucial for maintaining a stable environment.
For example, a small bakery decided to implement a detailed monitoring system for their cold storage. By keeping a log of temperatures and observing patterns, they were able to identify inconsistent readings, ultimately leading to the discovery of a faulty thermostat that required immediate replacement. The result? Improved efficiency, reduced energy costs, and preserved quality of their ingredients.
In conclusion, following consistent maintenance tips such as regular cleaning, defrosting, and diligently monitoring temperature levels can make a significant difference in the performance and longevity of cold rooms. Not only do these practices help prevent problems before they start, but they also ensure that businesses can thrive in a competitive and demanding environment. Rely on Emiratefix whenever repairs or expert advice is needed; they are committed to helping businesses maintain optimal conditions for their cold storage solutions.
Conclusion
Recap of Importance of Cold Room Repair
As we wrap up our discussion on cold room maintenance, it’s essential to highlight the critical role of cold room repair in the smooth operation of businesses that rely on refrigeration. The cold room is often the backbone of food safety, quality assurance, and operational efficiency. When cold rooms fail or falter, the repercussions can be significant — from spoiled inventory to safety violations, which negatively affect both finances and reputations.
Reflecting on the importance of cold room repair, several key points emerge:
- Food Safety Compliance: Regular repairs ensure that cold rooms maintain the required temperatures for food preservation, safeguarding against spoilage and contamination.
- Operational Efficiency: Well-maintained cold rooms run more smoothly, consuming less energy and reducing operational costs. Regular service can prevent energy wastage, improving overall profitability.
- Business Reputation: Maintaining cold storage means a commitment to quality, which builds trust with customers. A business known for its quality and safety stands to gain a competitive advantage.
- Avoiding Emergency Repairs: Proactive cold room repairs can prevent unexpected failures that might disrupt service during peak hours, ensuring that businesses can serve their clients without interruption.
As we have seen through various examples, the benefits of maintaining and repairing cold rooms extend far beyond immediate operational concerns. The investment in timely repair services pays dividends in reliability, safety, and cost savings.
Final Recommendations for Cold Room Maintenance
To ensure that cold rooms remain reliable and efficient, businesses should consider implementing some key maintenance practices:
- Schedule Regular Inspections: Make it a habit to conduct monthly inspections of cold rooms. Look for signs of wear, ice buildup, and overall cleanliness to catch potential issues before they escalate.
- Implement a Cleaning Routine: Establish a cleaning schedule that allows for thorough cleaning and defrosting on a regular basis. Implementing daily, weekly, and monthly tasks will keep the cold room in optimal condition.
- Daily: Quick surface clean-up and checking for spills.
- Weekly: Sweeping and mopping the floors, checking and cleaning vents.
- Monthly: Deep cleaning shelves, equipment, and performing extensive defrosting.
- Maintain Temperature Logs: Keep detailed records of temperature readings over time. Monitoring these levels can help detect fluctuations and potential malfunctions early, ensuring timely interventions.
- Train Staff on Best Practices: Ensure that all staff members are educated about the importance of cold room maintenance. Training on minimizing door openings and best practices for loading and unloading will contribute to overall efficiency.
- Partner with Professionals: Engaging experts from Emiratefix for repair and maintenance services can assure that cold rooms are managed effectively. Their knowledge, experience, and access to quality parts can make a significant difference to your operations.
- Utilize Technology: Consider investing in advanced monitoring systems that alert you to temperature and humidity changes. Technology can provide peace of mind and allow for quick responses to any issues.
In essence, prioritizing cold room maintenance not only fortifies the integrity of your storage solutions but also fosters a more efficient and sustainable operational environment. Choosing Emiratefix offers businesses the assurance of expert assistance and reliable services to keep their cold rooms in top shape.
As a closing note, remember that a proactive stance on cold room care translates to better food safety, cost savings, and ultimately, a more prosperous business. Regular repairs and diligent maintenance can help preserve the quality of assets and enhance customer satisfaction, ensuring that your business continues to thrive in a competitive marketplace. By following the outlined recommendations, businesses can make well-informed decisions that lead to a successful, safe, and efficient operation.
تعليقات (0)